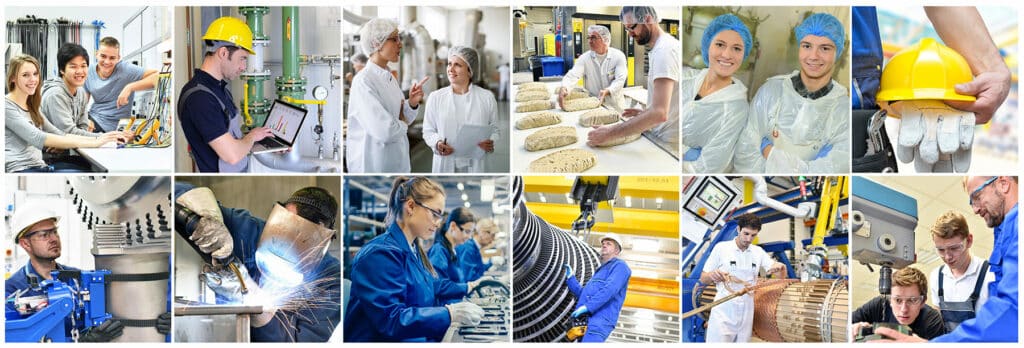
How to Efficiently Reduce Errors and Downtime in Manufacturing
Follow this three-step plan to dramatically decrease human errors while motivating and empowering your frontline workforce.
Nearly every finished product we encounter is the result of a complex manufacturing process. Many of the steps in that process are manual tasks performed by people. After all, despite factories being augmented with robots and algorithms, human hands are still needed to operate machines, program the robots, and give the finishing touches that make many products unique. But like anything human, all processes are prone to error.
The most common mistakes on the shop floor include:
- Errors resulting from lack of quality control standards.
When we don’t know what the definition of great is, we tend to make assumptions and subjective decisions. Both can be highly detrimental on the shop floor. - Errors in how production or assembly lines are set up. At this stage, operators typically go through a checklist to ensure all steps are tracked and implemented. If this checklist is unclear or, worse yet, if there’s no established process to guide the operator, the risk of deviation or error is very high.
- Measurement and counting errors. Even the best of us tend to go on auto-pilot when we perform a given task every day. An apathetic or complacent attitude is the greatest enemy of productivity and excellence.
1. Standardise
Standard Operating Procedures (SOP) are the foundation of a well-oiled manufacturing process. They provide standard guidelines for your team members to complete a given process. SOPs are often used to ensure that operations run smoothly: with cohesion, performance uniformity, and in compliance with safety measures and regulations.
- Having SOPs is essential to reduce manufacturing errors and downtime.
- Making them easily accessible and consumable through step-by-step digital instructions can go a long way to ensure they become the beating heart of your operations.
- Companies that transform this knowledge into dynamic instructions that are easy to update and access on the job can see First-Time-Right improve by up to 40%.
2. Train
On-the-job training is equally important to mitigate the risk of errors. Companies shouldn’t simply train new recruits and then forget about skill building. Most of the information gained in traditional onboarding and training is often insufficient or quickly forgotten.
- Learning on the job while collecting and providing regular feedback is a lot more effective.
- Build leadership skills among your most experienced employees and encourage them to mentor others in order to facilitate knowledge transfer.
- Foster a culture of continuous learning from the shop floor to further improve your procedures.
3. Motivate
Distrust, control, and micro-management are all human behaviours that can deteriorate collaboration and team spirit. Motivate instead of control. When your team is empowered with the right tools and encouraged to propose improvement ideas, they will be more engaged in their work
- Involve your team in shaping your standard operating procedures, so they can make meaningful contributions to the business.
- Create a strategy to capture your team’s knowledge and expertise and reward those who contribute. It’s ideas and feedback that drive continuous process improvement.